Photon Counting with High Speed vDAQ
With a sampling rate of 2.0 GHz to 2.7 GHz, the vDAQ-HS can record at sub nanosecond time resolution. The signal conditioning controls created exclusively for the vDAQ can bin photons collected with this high resolution into any of 32 virtual channels based on user defined temporal windows.
Hardware Setup
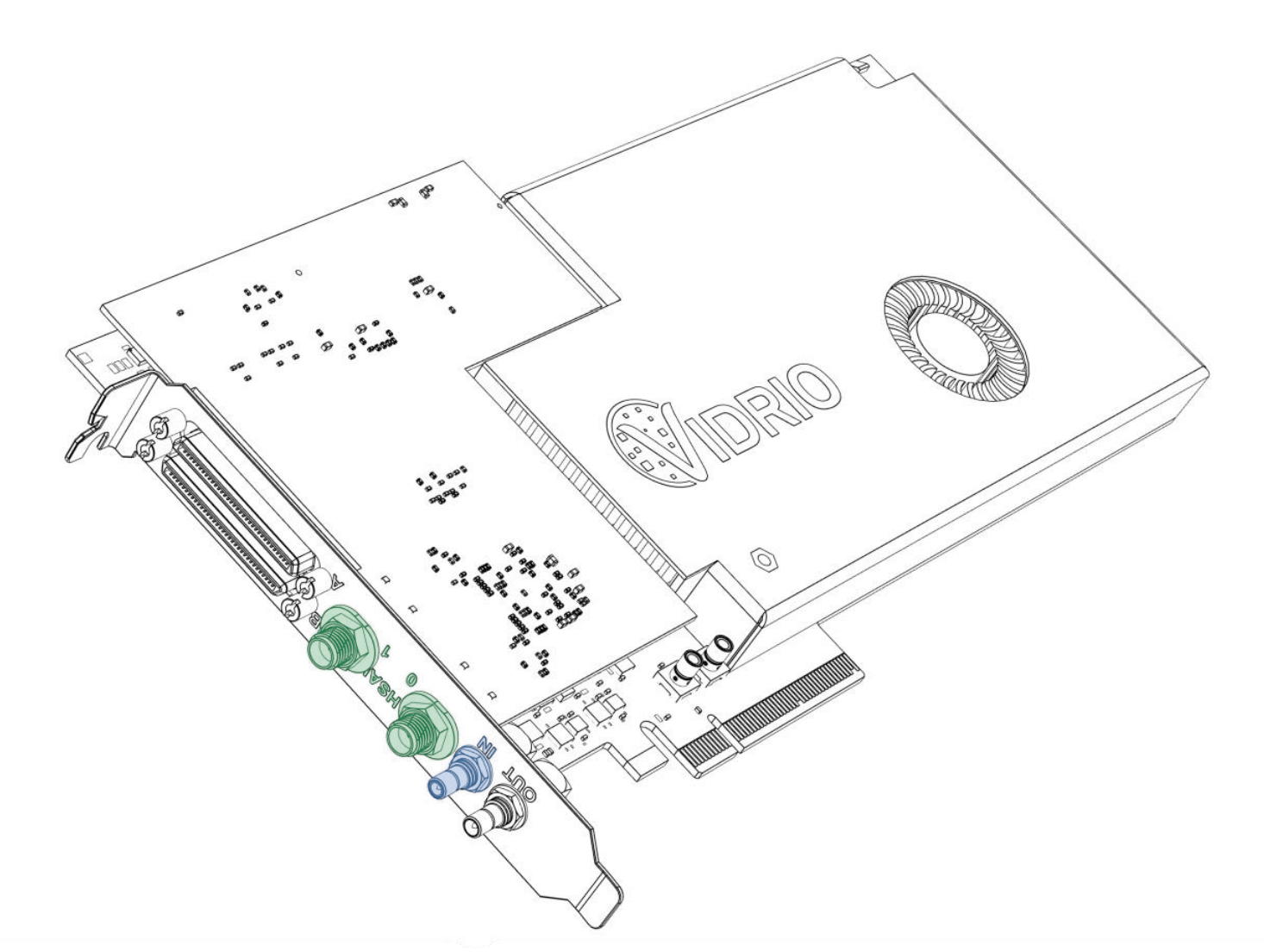
High Speed vDAQ
Connect amplified PMT signals to HSAI inputs highlighted green
(optionally) Connect a laser clock (62.5MHz-84.375MHz) to IN highlighted blue
The following hardware is used:
A fast transimpedance amplifier (bandwidth >80MHz) (such as the Femto DHPCA-100)
(optional) For time correlated photon counting with a laser rep rate less than 42.1875 MHz, a clock multiplier board such as the AD9516-0 is required
The high speed vDAQ is installed as is described in page vDAQ Installation.
Connect each Photomultiplier Tube (PMT) to the input of a separate high bandwidth transimpedance amplifier (TIA), and connect the the output of each TIA to the high speed analog inputs (HSAI) of the vDAQ. The ports are enumerated 0 and 1 on the vDAQ card’s PCIe bracket. Each are SMA male connectors; the cable from the TIA to the HSAI ports may need to be adapted from a different style connector on the TIA output.
Software Tutorial
Here, simple photon counting, virtual channels, and time correlated photon counting will be shown. Each topic builds from the previous.
Photon Counting
First, photon counting without synchronizing to the laser clock we be shown, and then time correlated photon counting.
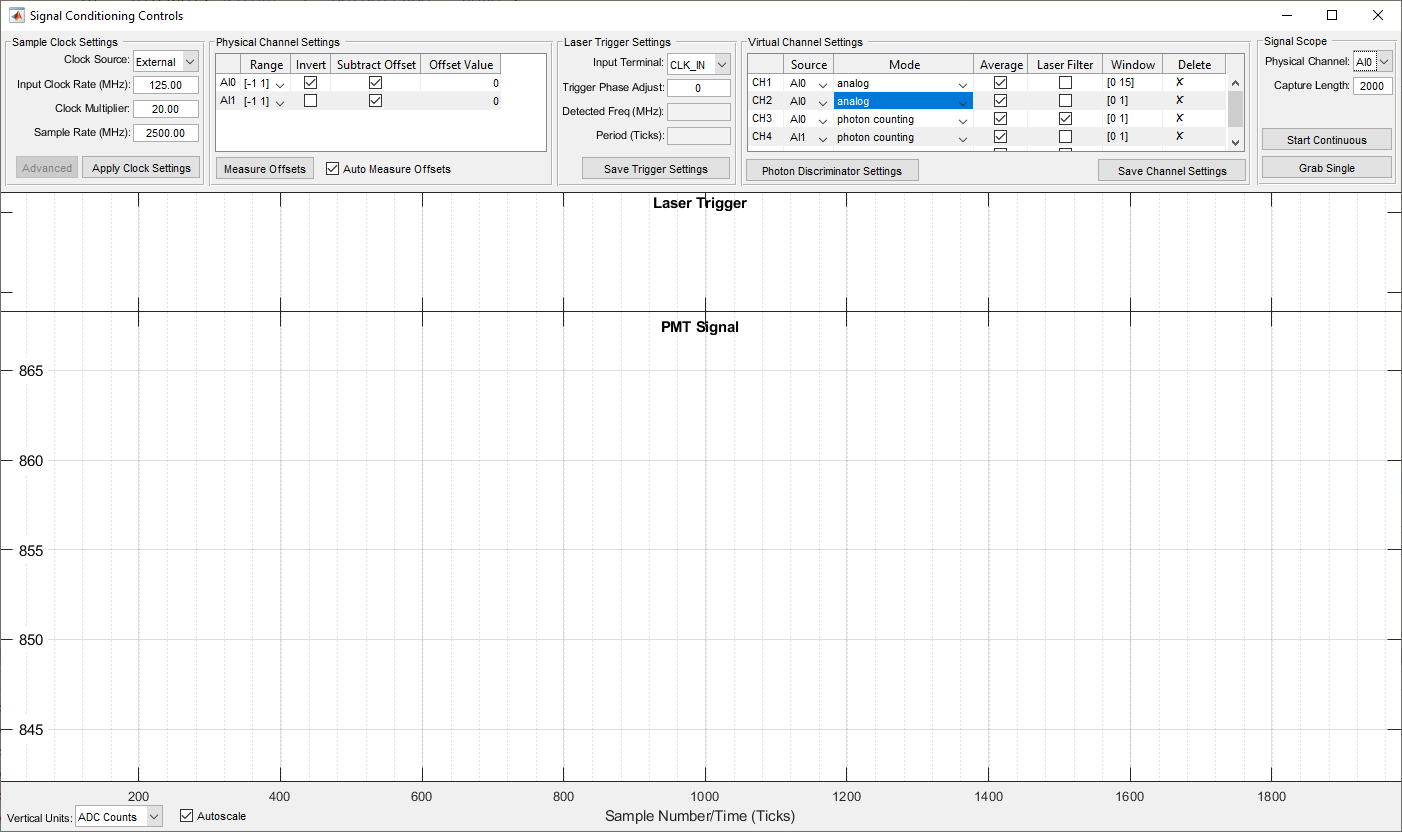
vDAQ Photon Counting is managed through the Signal Conditioning Controls window, which is summoned from Main Window>View>Signal Conditioning Controls. It is analogous to the Laser Trigger Scope used with NI hardware. It is only available when the currently selected imaging system (as selected from the configuration window) is a vDAQ Scan System.
Bring up the Signal Conditioning Controls window. First, notice the Signal Scope panel at the top right corner. The PMT signal can be monitored continuously, or a specified Capture Length can be grabbed. After preparing a sample where signal-to-noise ratio will be expected to be low and focusing at an appropriate depth, leave the acquisition in a Focus state and go back to the Signal Conditioning Controls GUI to press the Grab Single button.
This will populate the PMT Signal graph with data. From this data, decisions can be made on settings such as tolerances required for a peak to be counted as a photon. One can zoom in temporally by scrolling with the mouse wheel, or one can decrease the number of samples per grab, and do another grab.
the Virtual Channel Settings contains a table with a row per virtual channel. In the Mode column (column 3) of this table, the integration (analog) or photon counting data pipeline can be selected for each of the two SI channels.
The settings for determining how the photons are counted can be adjust now. Under the Threshold Crossing detection mode, any crossing of the threshold from below to above is counted as a photon. The dashed orange line represents the threshold, and it can be clicked and dragged to set a new threshold.
The threshold can also be set by typing in a value. To do this, click the Photon Discriminator Settings button, and edit the text in the box labeled Detection Threshold.
There is a second detection mode called Peak Detect. In this mode, a second plot is made from the original PMT signal called the Differentiated PMT Signal. This plot is made by simply taking a sample’s value and subtracting the sample value from a previous sample. The threshold is now applied to this differentiated PMT signal rather than the original.
The number of ticks separating these samples is known as the Differentiation Width, and is settable from the Photon Discriminator Settings.
Virtual Channels
With Virtual channels, several channels worth of image data can be saved from a common high speed analog input port. For example, SI channels 1 and 2 can each display input collected from HSAI1. Virtual channel 1 could use a photo integration pipeline where as virtual channel 2 could use a photon counting pipeline for the same PMT data.
In CH1 under the Source column column (row 1, column 2), one can specify that SI channel 1 should actually read the PMT signal from HSAI1 rather than HSAI0.
Up to 32 virtual channels can be added.
Virtual channels can be enabled to display or save from the Channels window.
To remove virtual channels, select delete in the Source column for the row of the virtual channel that should be deleted.
Note
The Image Controls window will remain with four channels regardless of the number of virtual channels. The channels in the image controls window correspond to physical channels. It will control which ADC counts correspond to zero and full brightness for the individual analog input ports.
In the case of the high speed vDAQ which has two high speed analog inputs, channels 3 and 4, do not control anything.
Time Correlated Photon Counting
If the sampling rate is synchronized with the laser rep rate, virtual channels can be used to bin samples by user defined temporal windows to separate out photons emitted by fluorophores with different fluorescent lifetimes. The windows are defined relative to each laser pulse.
First the external laser trigger must be configured. See the Sample Clock Settings. Set the Clock Source to External. Then set the input clock rate to the external clock rate (which must be between 62.5MHz and 84.375MHz). The Clock Multiplier must be 32; The resultant sampling rate should be between 2.0 and 2.7 GHz. In the laser trigger settings panel, set the Input Port in the Laser Trigger Settings panel to CLK IN. Finally, click Apply Clock Settings.
Verify that the laser clock frequency is measured correctly from the Laser Trigger Settings panel under Detected Freq (MHz).
The laser clock will now be overlayed on the PMT signal as dashed and solid red lines. Between the dashed and solid red lines will be a number of ticks equal to the Clock Multiplier. Windows can now be drawn over the PMT signal relative to the laser clock for each virtual channel.